Coordinated drive components for a
digitalized world
Siemens drive systems help increase uptime and minimize Total Cost of Ownership. Components are designed to work together seamlessly, delivering the most cost-effective, right sized drive system for any application. When supported by Siemens digitalization technology, productivity is enhanced and maintenance time reduced by quick and easy access to Siemens off-site technical resources.
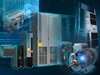
Siemens drive systems help increase uptime and minimize Total Cost of Ownership. Components are designed to work together seamlessly, delivering the most cost-effective, right sized drive system for any application. When supported by Siemens digitalization technology, productivity is enhanced and maintenance time reduced by quick and easy access to Siemens off-site technical resources.